COOLPULSE offers an economic solution for surface finishing of additive manufactured metal parts. By dissolving material from its parts surface, you can improve external and internal parts surfaces on multiple parts simultaneously. No matter if tool shops with the need for a single station, manually operated machine or automated solutions for production lines we are always possible to find the right solution for you.
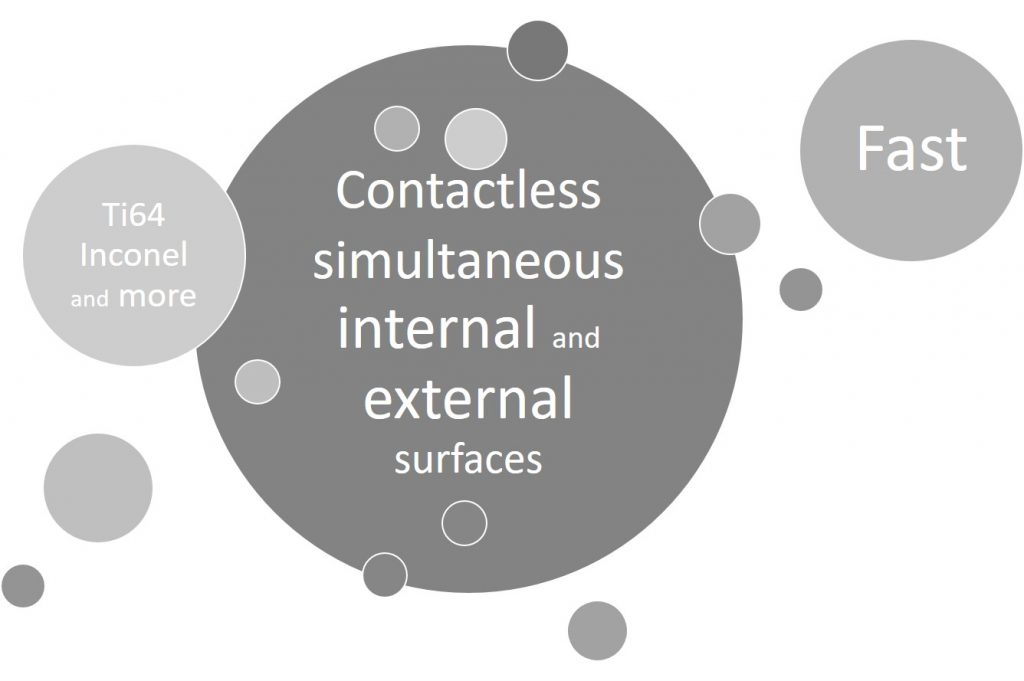
The COOLPULSE technology was originally invented for removing so called micro burrs. With Additive Manufacturing, and the increasing recognition of its benefits to products structure and freedom of design the awareness is dramatically increasing. Especially in segments as aerospace and medical, where the customization of the parts is either crucial, or the production volumes are rather low, Coolpulse took root in the market and became recognized as a technology for serial production. But all market players are facing the same challenges. Especially when it comes to functional surfaces there is no economic way to achieve an acceptable surface finish with an economic use of resources. Therefore it will become more and more important to also focus on the finishing process and its properties during the design stage in a project, to achieve an optimized AM process chain, not only cost wise, also quality wise.
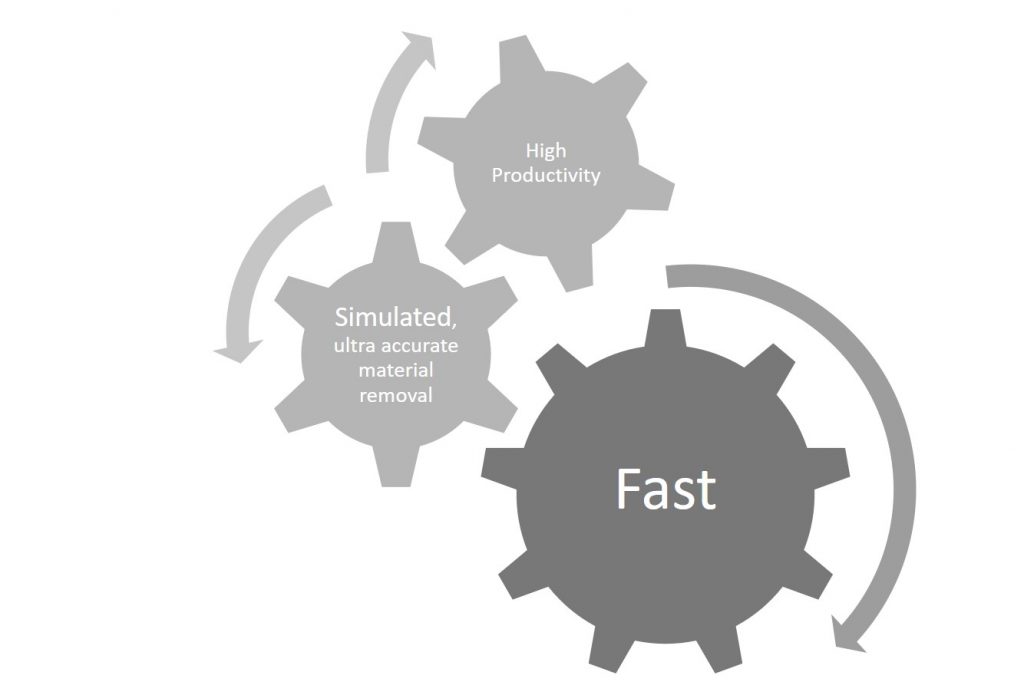
COOLPULSE falls under the category of the Anodic Metal Dissolution Technologies, like Electro Chemical Machining (ECM). The component is machined by utilizing a tool that mimics the surface geometry of the 3D printed component. The printed part is connected to a positive electric pole (anode), and the printed tool is connected ta a negative electric pole (cathode). The surface of the printed part is machined by running an electrolytic solution between the parts, while driving a controlled DC current between the part and the tool. The applications are categorized into two different modes. One is called “Bath” technology, where very simple cathodes can be used, but the machining is limited to deburring and finishing applications on external surfaces and cavities with an aspect ratio < 0.5, and “Tooling” technology, where a part specific tooling ensures uniform and high-class surface finishing on external, as well as on internal surfaces.
> Creates a defined surface structure at both the micro and macro level for the workpiece.
> Reasonable and controllable stock removal.
> Polishing effect on the surface internally and externally.
> Removes remaining defects from the support structure and surface.
> High current density on peaks and edges of the work-piece allows for consistent edge rounding.
Thanks to a flexible offering and global foot print, we can assist you via our state-of-the-art centers of excellence in China, Europe, India, Japan, United Kingdom and United States.
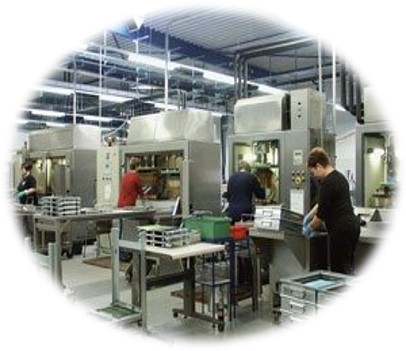
Contract Shop
Flexible, scalable, certified. Leverage cutting-edge expertise without upfront investment.
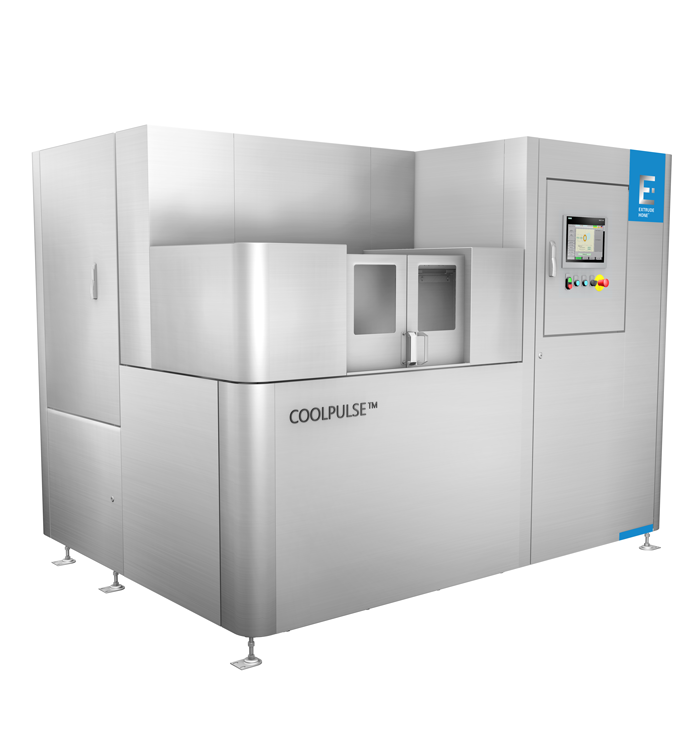
Equipment
Discover our COOLPULSE™ equipment offering and technical specification on Extrude Hone website.